
#Grbl controller 3.5 Pc#
This works very straight forward but needs a PC to keep a stream of Gcode commands running to the USB controller. I also have an original USB Mach3 interface with a. I use this for my small 3018 CNC.ĥ) GRBL, Estlcam& Openscad & Mega2560 & RAMPS 1.6 shield. The nice option of this setup is the 3.5 inch LCD that also comes preconfigured for CNC. But- this is a very neat solution for smaller machines. Still investigating this…Ĥ) GRBL, Estlcam & Openscad & MKS DLCV2.1 board with TFT 3.5 “ Also for this setup: No option for squaring the dual Y axis setup. This is actually a very solid and reliable solution BUT I could not get it to do any way of squaring my dual Y axis setup. The second thing that prevents me from going this way is the fact that it proved impossible to have a functional LCD attached that shows things like position, speed, status et cetera.ģ) Mach3, FreeCad & USB CNC ‘barebone’. The main reason to NOT use this is the fact that the GT2560 board just has not got enough pins available onboard for things like a handwheel and other outputs for accessories.
#Grbl controller 3.5 driver#
nc files…, using the machine configuration to get the code properly generated for the Indymill’s dimensions and hardware settings)Ģ) GRBL, Estlcam & Openscad, Marlin & GT2560 (A) board This is also working out of the box and emulates a GRBL driver board.
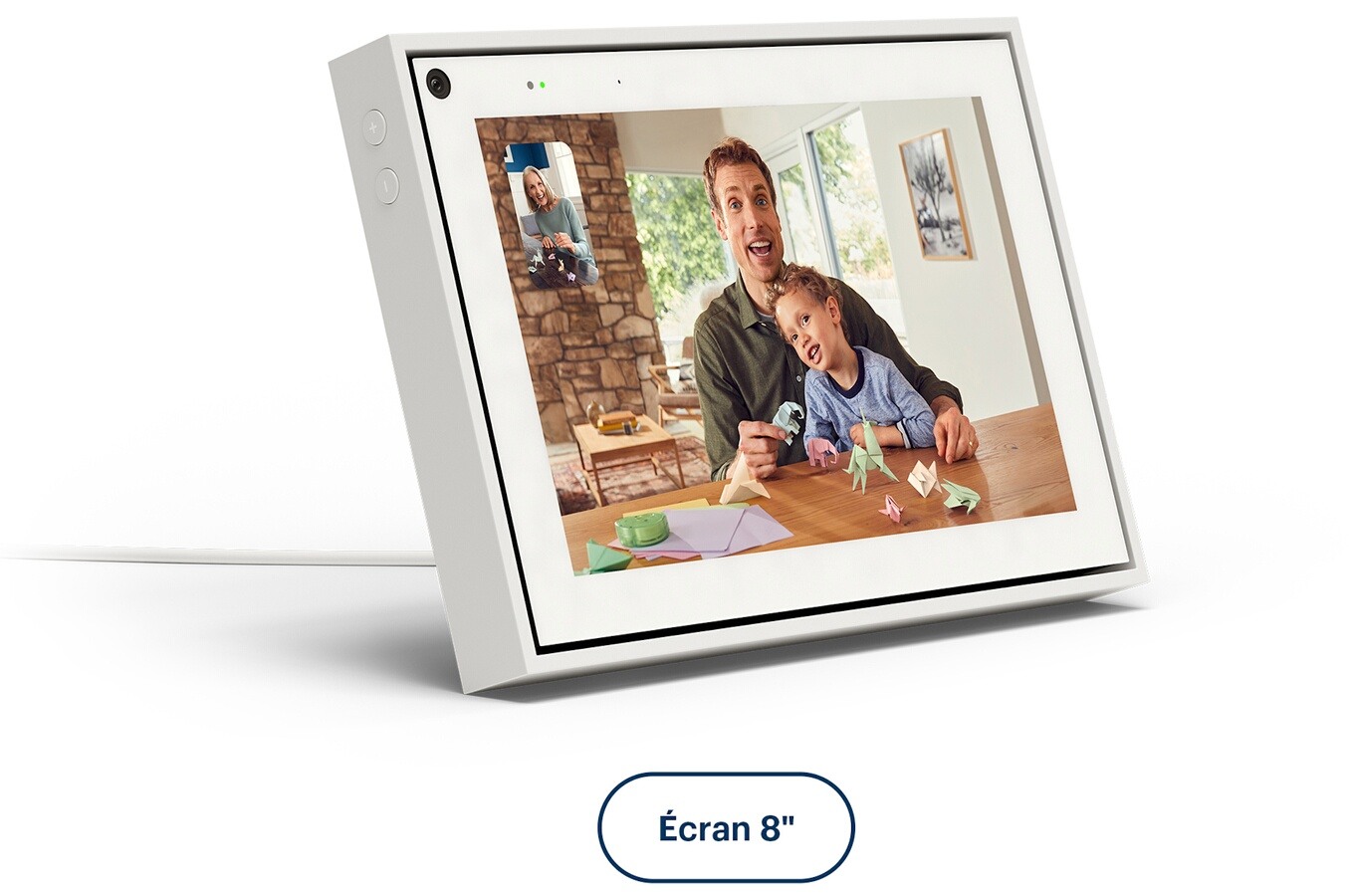
(I make my designs in Openscad and save this as. I also learned that Estlcam can generate Gcode that I can then send via the webinterface to the Indymill CNC machine which works very well. the webinterface and the ease of having an automatic squaring gantry on the 2 Y axes with individual endstops. I still have this setup as backup and by switching the connectors from the Indymill over, I can easily switch to this setup. Actually, the Duet reprap CNC setup is very mature and customizable. And dual axis squaring is also easily made possible.
#Grbl controller 3.5 serial#
It is, however, possible to attach a serial handwheel to the Duet2wifi and manually control the CNC setup. Not chosen by me beacause it proved impossible to run a gcode stream online from the PC to the USB interface of the Duet2wifi board. The Gcode is then uploaded via Duet webinterface and run on the local reprap driver board. STL’s are made with OpenScad and then converted either online or with Estlcam to Gcode (.nc files). To get the best possible CNC driver / firmware setup, in combination with the CAD and CAM programs that are required, I tested the following setups with the Indymill hardware:ġ) Reprap 3.3 & the Duet2wifi.
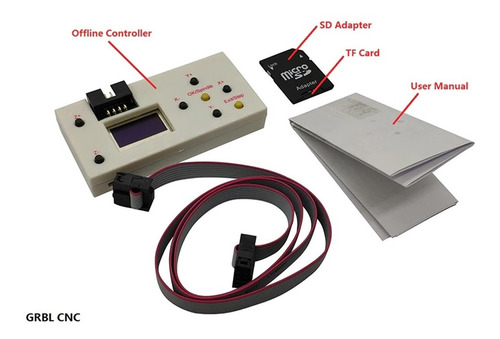
Wobbling in cheap linear bearing screws.Plasma cutter router DIY ‘the simple way’.Disc brakes for my Citroën Traction Avant.Are professional 3d printers overpriced?.
